How do we implement the circular economy today?
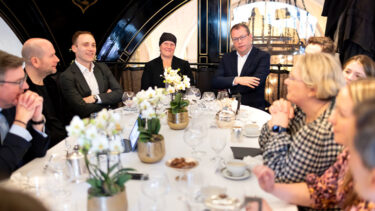
Senior members from the built environment attended a roundtable event hosted by Wates in March to share learnings about how their businesses are implementing circular economy principles today and how to bring it into the mainstream. Here’s what they discussed.
25 July 2024, known as ‘Earth Overshoot Day’, is the date this year humanity will have exhausted nature’s resources for the present year, compared with the speed they can be regenerated.
This sobering thought formed the backdrop to a roundtable discussion hosted by Wates. With construction, demolition, and excavation accounting for 60% of material use and waste generation in the UK, according to the UKGBC, senior industry members gathered to explore how their businesses are implementing the circular economy and what’s needed for further adoption.
The circular economy is one of the key ways the sector can limit its impact and is based around three core principles: maximising asset reuse and recovering materials; minimising waste; and design for optimisation. Kick starting the discussion, Wates Construction London Regional Director, Mark Craig, asked what constraints people are currently experiencing when trying to implement these principles.
“There are lots and lots of constraints,” began British Land Sustainability Manager, Emily Samoluk, which was met with a lot of nodding heads around the table. “On a project level, these buildings were not designed with the circular economy in mind. Going forward, we’re ensuring design for disassembly is built into the project scope.”
Head of Sustainability at Cadogan, Sarra Pardali said that while businesses have made a huge amount of progress in embedding sustainability in their operations, they still required more certainty from government. Commercial viability was also flagged as a barrier, with Wates Construction Design Director, Paula Chandler, asking how the sector can better sell commercial viability by “doing the right thing” and opting for sustainable solutions and delivery.
“This is a really interesting point,” responded Rider Levett Bucknall Partner and Public Sector Cost Management Lead for London, Gemma Prior. “Because as a Cost Manager, quite often doing the right thing doesn’t always save money.”
Orms Architectural Associate, Rachel Hoolahan, questioned how the wider supply chain could be involved. “Currently it’s cheaper to quarry new resources, potentially from the other side of the world, than it is to reuse materials. Is this something the supply chain needs to improve on?”
This turned the attention to McGee Head of Carbon, Charlie Wedgwood, whose demolition company carries out pre-demolition audits when assessing what materials can be reused onsite. He said there was a current risk perception for certain elements of deconstruction and concerns around the impact on programme. “But there are different ways where we can target some deconstruction whilst keeping everything else moving [onsite], to avoid it becoming expensive.”
From there, the conversation moved to better sharing of materials for reuse and what was required from a storage perspective. This prompted Mark Craig to question whether clients could collaborate. “Some clients obviously have quite a few projects on the go, so they’ve got more overreach in terms of what they can do from a deconstruction or material saving point of view, and how they can reuse that elsewhere. So, is there room for a collaboration between clients to share and reuse materials?”
This animated the room, with Emily Samoluk pointing out an example where British Land sourced reclaimed access flooring from Stanhope, and Rachel Hoolahan saying Orms Architectural were approached regularly with ideas for materials hubs.
Early engagement and rethinking business models
Ramboll Principal Sustainability Engineer and Circular Economy Expert, Kaspar Bajars, observed how early engagement with the insurance sector could reduce risk perception. “We’ve had discussions with insurers and their point is that the majority of risks are perceived,” he said. “If you communicated with insurers early, even in RIBA stage 1, they could tick off which risks are actual. This drives down insurance costs, improves transparency, and generally everyone in the project team has more certainty around design regarding use of reclaimed materials and systems.”
The discussion moved on to the role of legislation, with Waterman Structures Director, Charlie Scott, proposing a reverse VAT mechanism to incentivise material reuse. He said: “We’ve got to find a UK mechanism that makes this a cost-effective default rather than the virtuous alternative.”
Wates Group Sustainability Director, Cressida Curtis, said policy had moved on considerably in the last 10 years, but industry shouldn’t rely on government to drive the agenda forward. She suggested looking to the finance sector instead as they are “desperate to decarbonise their own loan books” and “construction would find quicker solutions by understanding the financial mechanisms.”
The conversation ended on how the sector can harness the power of data and digital application to follow what Paula Chandler referred to as the “green thread”. Orms Architectural Director, Colin McColl highlighted his business’ work around material passporting and tying that to digital twins. “Data is only as good as the information inputted and what you do with it,” he said. “A lot of our work’s around making that interface easy and manageable.”
A materials passport gathers and organises data about the materials within a building to better enable its reuse. On this, he added: “We try to have an open-source approach. We want to learn from industry mistakes and share them openly with a positive attitude.”
Fletcher Priest Associate Partner, Joe Sweeney, added that his business was using digital twins “as standard on most projects”, but questioned what happens to that information once the project is handed over. “I know the complexity that goes into it from the team, so the developers, clients, or whoever need that equivalent team to continue it.”
Ramboll’s Head of High Rise and Complex Buildings team, Tom Shaw, echoed this idea of collective working, in what was a fitting final thought for the day. “The skill set is there, we employ engineers that can now code, we’re writing and creating digital tools for every day applications including sustainability enabling us to go further faster with our assessments,” he said. “But actually, it’s about honing down that skillset and combined ambition because I think everyone is still protecting their IP a little bit, working in silos, and reinventing the wheel. It’s about getting into that mindset of sharing knowledge and the lessons learned of where we have done well and not so well. We need to get better together.”