A unified approach is key to the long-term success of offsite
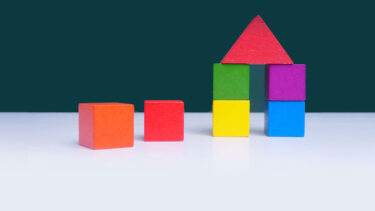
The profile of offsite has never been higher and yet despite it being far from a new concept, there remains significant discussion about how the industry can more effectively deliver what would appear to be its obvious potential.
This was the key topic at the Wates Construction Summer Series that brought together a range of experts to discuss hot topics in the industry. Andrew Barraclough, Group Design Director at Wates Construction, shares the outcome of the discussion in the blog below.
Andrew Barraclough
Design Director, Wates Construction
It was acknowledged that there needs to be an industry-wide agreed definition and a common calculation to make PMV truly meaningful.
The consequence of not having a common approach across the industry is that we don’t have the clear data to properly evidence the benefits of offsite. As one panellist stated, we are told that MMC is 30 per cent quicker, but quicker than what?
This lack of data was highlighted as a potential barrier to the cultural change necessary to fully embrace the opportunities of offsite. Hearts and minds needed to be persuaded and that would only happen when it was clear what the tangible and measurable benefits were.
In some sectors such as education, there is little argument about the benefits of offsite. Wates currently sits on the Government’s £3bn MMC framework and has delivered more than £900m of projects over the past decade using our Adapt ‘kit of parts’ approach. The outcomes are comparable if not better than those delivered via more traditional methods.
It is pioneering sectors like education that are going to play a huge role in taking the construction industry forward when it comes to adapting and integrating offsite because the minimum PMV requirements for future public frameworks are sure to increase, leaving behind those that have not adapted to the new reality.
The clear consensus from the discussion was that a standardised approach to PMV is going to be critical in construction’s ongoing evolution if it is going to capture the efficiencies the industry so desperately needs, although it is not the only challenge that needs to be overcome.
Another was that slightly counter intuitively, the cost of embracing the opportunities of offsite can be restrictive because it means more investment in consultants up front when the funding of many projects is weighted towards after a project has achieved planning.
Engaging with contractors at a far earlier stage than is often the case is also absolutely essential so that the offsite opportunities can be properly understood from the outset and become part of the initial design process rather than considered retrospectively, adding additional cost and diminishing the efficiency premium.
What seems clear is that for the promise of offsite to be realised, a clear strategy with realistic goals needs to be established with a top down mandate that will explode the myths around offsite and drive the necessary cultural change that will fuel this latest stage in the evolution of our industry.